In the 18th century the invention of die casting - a casting process involving forcing molten metal under high pressure into a mould cavity - was one of the most outstanding advances in the printing industry, and is now standard in the manufacturing of tools and other components.
At that time, die casting was focused on the production of letters and punctuation marks for movable typewriters. The process made it possible to produce the same dimensions down to the last detail while saving time on set-up.
In 1890, following this groundbreaking success, other uses were found for products made by die casting and people realized how easy it was to produce complex constructions using this method. The common raw materials for the die casting process were lead and tin. However, over time, more and more people came to the conclusion that these materials were not safe due to toxic ingredients, and people later switched to resources such as aluminium, zinc, copper, and magnesium. These raw materials offered a wide range of advantages: in addition to being safer, they were more heat resistant and stable than the materials used previously.
The current state of the die casting industry & latest developments
Nowadays, we mainly make use of the so-called high-pressure die casting process and thus achieve numerous other advantages. The use of high pressure has allowed us to develop products of even better quality, to make the parts more robust and to address completely new industries (currently, the automotive industry is the largest consumer of products made by die casting). In addition, the tools and components can now be welded and glued, and the surfaces can be adapted to specific uses. In addition to the automotive industry mentioned above, there are now customers in the transportation, manufacturing and construction sectors.
If you would like to know more about the die casting method and the process along with it, check out this video by Engineeringdotcom before we go on about the recent developments, benefits of die casting etc.
The pandemic in correlation with die casting
Even though the pandemic had a significant impact on the die casting industry due to supply chain restrictions and trade limitations, among other factors, the market recovered quickly, and experts anticipate exponential growth within the die casting industry. There will be ever-increasing demand, particularly in the manufacturing process of industrial machinery and the electronics industry. In this context, production with aluminium will continue to gain popularity, mainly due to the fact that almost 35% of manufactured vehicles are made of aluminium.
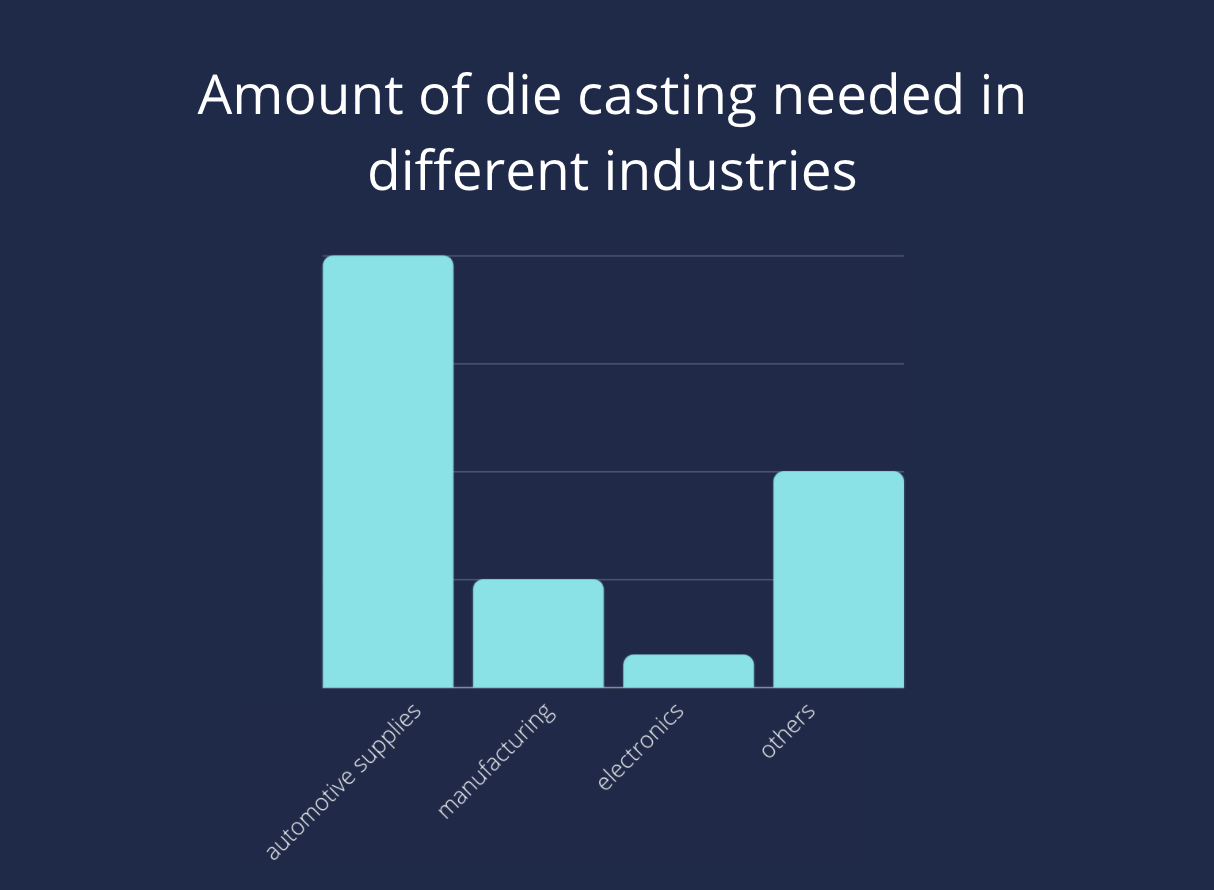
Top 5 most successful companies in the die casting industry
Nemak is a global company specializing in automotive parts (mainly aluminium). It is one of the 60 largest and most successful companies in the world.
Rheinmetall produced (un)armored wheeled vehicles for security and armed forces until recently but has been focusing on military-specified vehicles since 2019.
GF Casting Solutions is one of the leaders in manufacturing technology and focuses on the
transportation of gases as well as liquids.
Shiloh focuses on the manufacturing and optimization of powertrain systems, body structure and interior systems using lightweight multi-material solutions.
Ryobi is a Japanese brand of Techtronic Industries that mainly pays attention to the automotive and electronics industries.
Advantages of die casting
The production of tools and components by the die-casting process offers many attractive advantages that companies can take advantage of, especially in the automotive, manufacturing and electronic equipment development industries. For example, working with die casting ensures the highest quality of manufactured products and makes it possible to produce complex and multifunctional tools that are much more robust than similar products made of plastic. This effectively saves time and, consequently, money. In addition, working with die casting makes it possible to produce a large number of identical products, which, if necessary, can also be manufactured with smoother surfaces than with other casting processes. Further advantages are offered by the possibility, for example, of making holes, threads and bolts in the component, which in turn reduces the cost of assembly work.
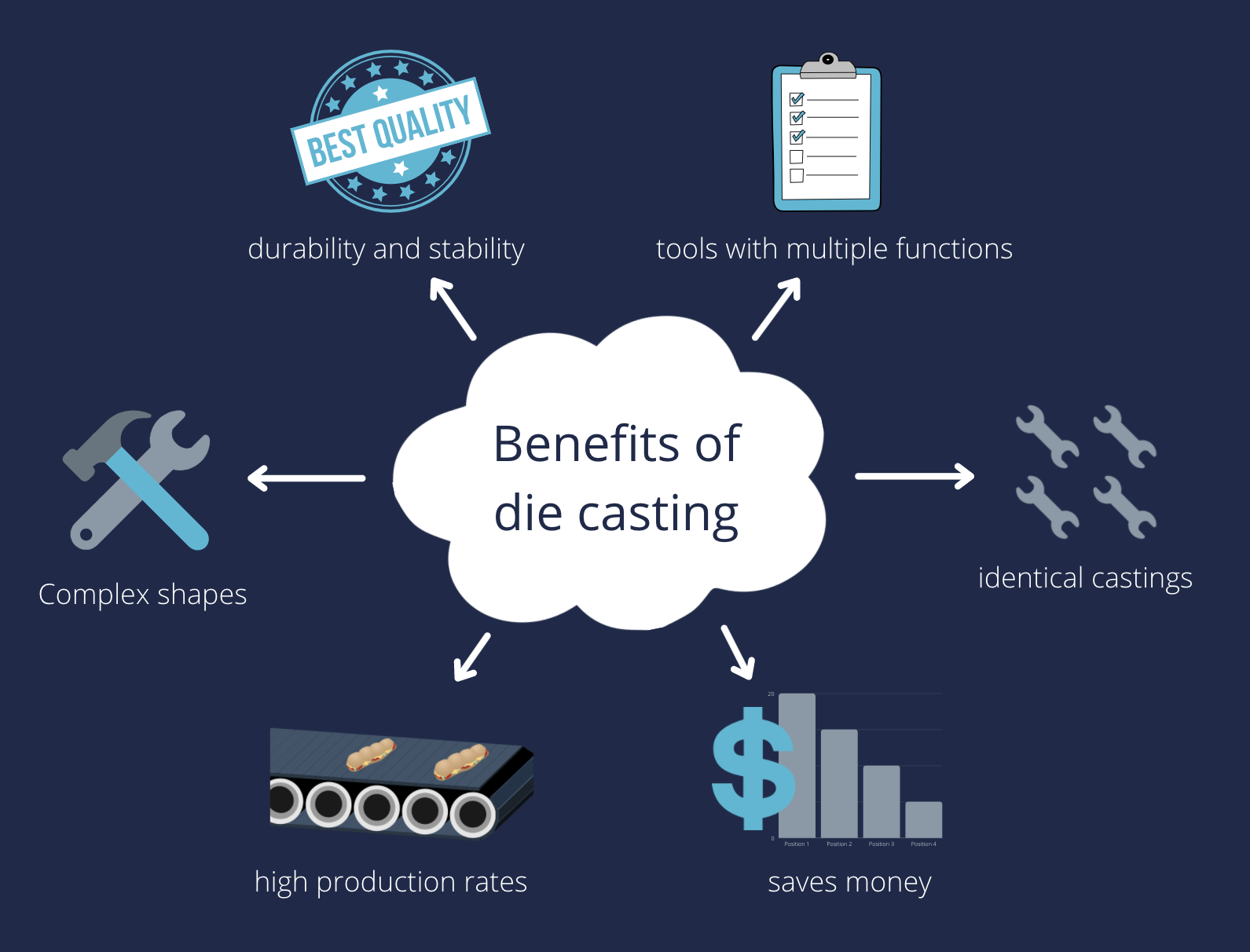
The future of the die casting industry
In 2020, the die casting industry was estimated to have a market value of approximately $57 billion, and experts calculated that this substantial sum will increase to just over $81 billion by 2026. Among them, China is the top producer and marketer of $37 million worth of refined aluminium. In comparison, Europe only reaches about $3.8 million.
Based on the statistics around die casting broken down above, it looks like a bright future for the industry. However, even this does not come without certain difficulties; the biggest obstacle is expected to be the growing popularity of e-vehicles. The combustion engines commonly used to date will eventually be phased out altogether, so the main focus in the near future will be on the environmentally friendly alternative. Fortunately, there will also be significant demand for components produced by die casting, as the demand for lightweight components will continue to rise.
Conclusion
Working with die casting has revolutionized our industry, allowing manufacturers to work more efficiently, save on costs and give a whole new meaning to the word "mass production" in engineering. Even during the pandemic, business was comparatively good, and the industry quickly recovered from the economic obstacles caused by Corona. Suppliers in the automotive industry are increasingly benefiting from the methodology invented over 300 years ago, and the die casting business is also expected to do extremely well in the future, offering high potential for manufacturers worldwide.
Die Erfindung der Druckguss-Methodik im 18. Jahrhundert war einer der herausragendsten Fortschritte der Druckereibranche und ist heute Standard bei der Herstellung von Werkzeugen und Bauteilen. Damals fokussierte man sich bei der Arbeit mit Druckguss zunächst auf die Herstellung von Buchstaben- und Satzzeichenstiften für bewegliche Schreibmaschinen. Das Verfahren machte es möglich, die gleichen Maße detailgenau zu produzieren und dabei Zeit bei der Produktion zu sparen.
Im Jahr 1890 wurden nach diesem bahnbrechenden Erfolg auch andere Verwendungszwecke für die durch Druckguss hergestellten Produkte gefunden und man erkannte, wie einfach es war, komplexe Konstrukte mithilfe der Methode herzustellen. Die gängigen Rohstoffe für das Druckgussverfahren waren Blei und Zinn. Im Laufe der Zeit erkannte man jedoch, dass diese Materialien aufgrund toxischer Inhaltsstoffe gefährlich waren und man stieg später auf Ressourcen wie Aluminium, Zink, Kupfer und Magnesium um. Diese Rohstoffe boten eine ganze Reihe von Vorteilen: Abgesehen von den weniger giftigen Inhaltsstoffen waren Sie hitzeresistenter und stabiler gegenüber ihren Vorfahren und überzeugten auch in der Herstellung komplexer Bauteile.
Der aktuelle Stand der Druckgussbranche + neueste Entwicklungen
Heutzutage macht man hauptsächlich Gebrauch vom sogenannten Hochdruckgussverfahren und erreichen damit zahlreiche weitere Vorteile. Durch den Einsatz von Hochdruck konnten wir Produkte von noch besserer Qualität entwickeln, die Teile robuster machen und komplett neue Branchen ansprechen (Aktuell ist die Automobilindustrie der größte Abnehmer der durch Druckguss erzeugten Produkte). Außerdem sind die Werkzeuge und Bauteile mittlerweile verschweißbar, können geklebt werden und die Oberflächen können immer besser an die jeweiligen Verwendungszwecke angepasst werden. Neben der oben erwähnten automobilen Industrie gibt es mittlerweile Abnehmer in den Bereichen Transport, Manufaktur und Konstruktion.
Wenn Sie mehr über das Druckgussverfahren und den damit verbundenen Prozess erfahren möchten, können Sie sich dieses Video von Engineeringdotcom ansehen, bevor wir auf die jüngsten Entwicklungen, die Vorteile des Druckgusses usw. eingehen.
Die Pandemie im Zusammenhang mit Druckguss
Auch wenn die Pandemie unter anderem aufgrund von Beschränkungen der Lieferkette und Handelsbeschränkungen einen signifikanten Einfluss auf die Druckgussindustrie hatte, erholte sich der Markt schnell und Experten rechnen mit exponentiellem Wachstum innerhalb der Druckgussindustrie. Vor allem in der Herstellung von Industriemaschinen und der Elektronikindustrie wird es eine immer größere Nachfrage geben. Dabei wird die Produktion mit Aluminium weiter an Popularität gewinnen, was hauptsächlich daran liegt, dass fast 35 % der hergestellten Fahrzeuge aus Aluminium bestehen.
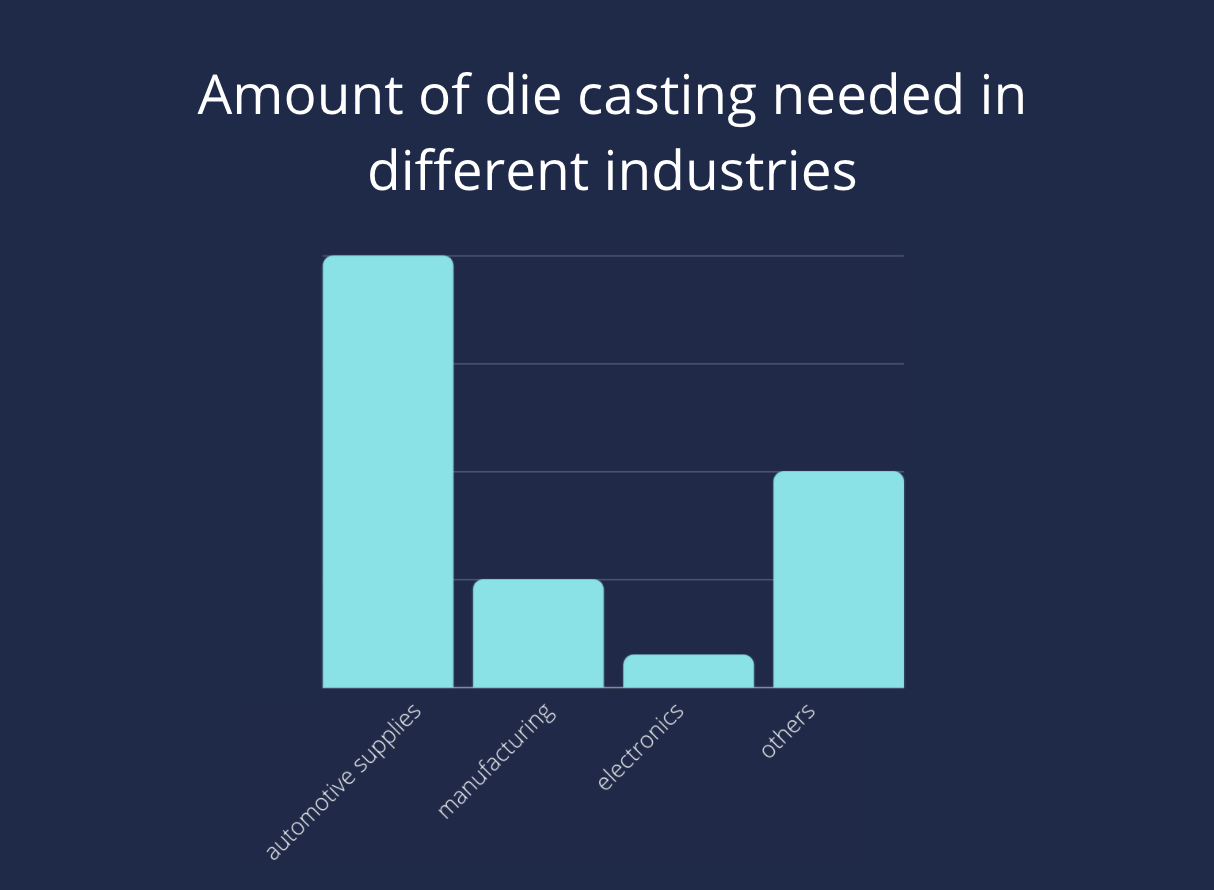
Top 5 der erfolgreichsten Unternehmen in der Druckgussbranche
Nemak ist ein weltweit tätiges Unternehmen, das sich auf Kfz-Teile (hauptsächlich aus Aluminium spezialisiert. Es ist eines der 60 größten und erfolgreichsten Unternehmen der Welt.
Rheinmetall stellte bis vor Kurzem bevorzugt (un)gepanzerte Radfahrzeuge für Sicherheits- und Streitkräfte her, fokussiert sich aber seit 2019 auf militärspezifizierte Fahrzeuge.
GF Casting Solutions ist eines der führenden Unternehmen im Bereich Fertigungstechnologie und konzentriert sich auf den Transport von und Gasen sowie Flüssigkeiten.
Shiloh fokussiert sich auf die Herstellung und Optimierung von Antriebsstrangsystemen, Karosseriestruktur und Innenraumsystemen durch den Einsatz von leichten Multimateriallösungen.
Ryobi ist eine japanische Marke von Techtronic Industries, die hauptsächlich im automobilen Bereich und der Elektronik-Industrie fungiert.
Vorteile von Druckguss
Durch die Herstellung von Werkzeugen und Bauteilen durch das Druckgussverfahren gehen viele attraktive Vorteile einher, die sich Unternehmen vor allem in der Automobilindustrie, Manufaktur und der Entwicklung elektronischer Geräte zunutze machen können. Z. B. gewährleistet das Arbeiten mit Druckguss höchste Qualität der hergestellten Produkte und macht auch die Herstellung komplexer und multifunktionaler Werkzeuge möglich, die viel robuster sind als ähnliche Produkte aus Kunststoff. So kann effektiv Zeit und damit auch Geld gespart werden. Darüber hinaus ermöglicht die Arbeit mit Druckguss eine Vielzahl an identischen Produkten herzustellen, die bei Bedarf auch mit glatteren Oberflächen hergestellt werden können als bei anderen Gussverfahren. Weitere Vorteile bietet die Möglichkeit, z. B. Löcher, Gewinde und auch Bolzen in dem Bauteil anzubringen, was wiederum die Kosten bei den Montagearbeiten senkt.
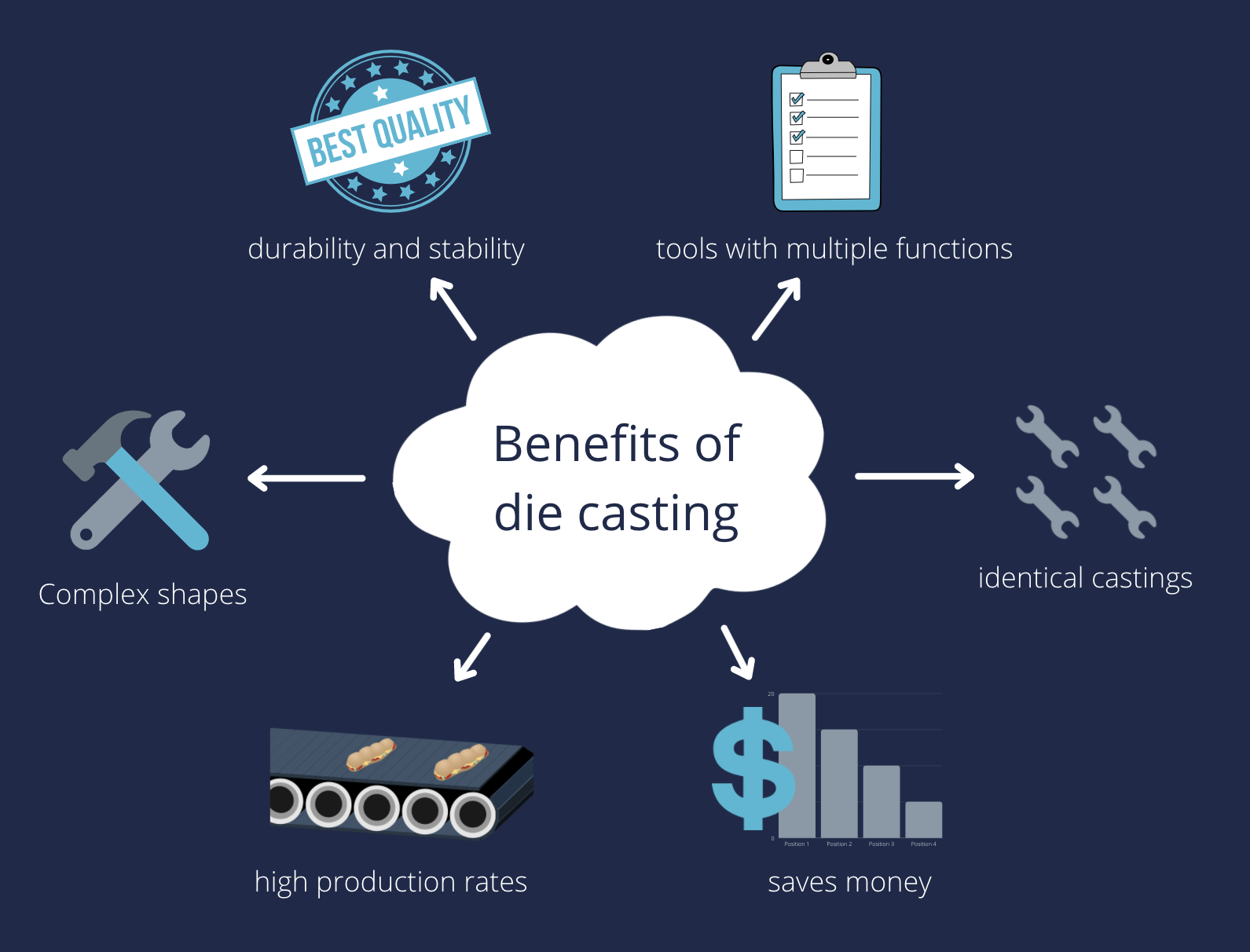
Die Zukunft der Druckgussindustrie
Im Jahr 2020 wurde die Druckgussindustrie auf einen Marktwert von ca. 57 Milliarden $ geschätzt und Experten berechneten, dass diese beträchtliche Summe bis zum Jahr 2026 auf knapp über 81 Milliarden $ ansteigen wird. Darunter ist China Spitzenreiter in der Produktion und der Vermarktung von raffiniertem Aluminium im Wert von 37 Millionen $. Im Vergleich erreicht Europa nur ca. 3,8 Millionen $.
Basierend auf den oben aufgeschlüsselten Statistiken rund ums Thema Druckguss sieht es nach einer rosigen Zukunft für die Industrie aus. Allerdings kommt auch diese nicht ohne gewisse Schwierigkeiten: Das größte Hindernis wird dabei voraussichtlich die wachsende Popularität an E-Fahrzeugen darstellen. Die bisher gängigen Verbrennermotoren werden irgendwann ganz abgeschafft, deshalb gilt es, sich zeitnah hauptsächlich mit der umweltfreundlichen Alternative auseinanderzusetzen.
Erfreulicherweise wird es auch hier signifikante Nachfrage nach durch Druckguss erzeugten Bauteilen geben, da die Nachfrage an leichten Bauteilen weiter ansteigen wird.
Fazit
Die Arbeit mit Druckguss hat unsere Industrie revolutioniert und es Herstellern ermöglicht, effizienter zu arbeiten, an Kosten zu sparen und dem Wort “Massenproduktion” im Engineering-Bereich eine völlig neue Bedeutung zu geben. Sogar während der Pandemie lief das Geschäft vergleichsweise gut und die Industrie hat sich schnell wieder von den wirtschaftlichen Hindernissen durch Corona erholt. Gerade Zulieferer in der automobilen Industrie profitieren zunehmend von der vor über 300 Jahren erfundenen Methodik und auch in Zukunft wird das Druckgussgeschäft voraussichtlich hervorragend laufen und ein hohes Potenzial für Hersteller weltweit bieten.